Resources
Testing Infrastructure
Charybdis LLC has worked closely with Florida Atlantic University’s Southeast National Marine Renewable Energy Center (SNMREC) since 2016, developing prototype open ocean MHK, and more recently, river-based generator systems. During this relationship, several testing devices have been built to support these efforts. A specially designed test barge and frame, collectively named the Rotor Testing Device (RTD), was built in 2016 to enable in-water device testing in the sheltered waters of FAU’s Harbor Branch Oceanographic Institute (HBOI) in Fort Pierce, Florida. The RTD project was funded by SNMREC and the State of Florida’s Renewable Energy and Energy-Efficient Technologies (REET) program.
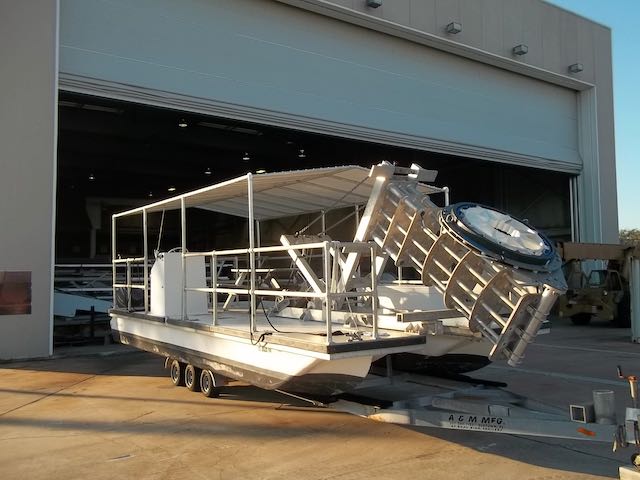
Rotor Testing Device
The barge is a dual-hulled vessel with a large open section at the bow that allows a test frame to rotate into the water at the bow of the boat. The frame was designed to hold various generator components, including axial rotors, single blades, and a variety of other novel devices. Initially, the barge and frame were used for conventional rotors up to 3 meters in diameter, for both static and rotating performance. In the last few years, the frame was updated to support single blade testing, as well as a 1-meter diameter river generator test item composed of four 1-meter blade sections connected to a coin generator (CG).
The deployment frame of the RTD is capable of pivoting from a position out of the water for transiting and device access to a vertical position with the generator rotational axis at a depth of 3.5 meters. This permits rotors up to 3 meters in diameter or one meter in length in regards to the river device to be pushed through the water at specific speeds. The forward location of the frame and test device avoids the water turbulence typical of towed and stern or side-mounted testing devices, providing a smooth and consistent flow over the devices. The barge is also reinforced to support the frame, as well as a small davit for equipment handling at the bow. The large deck (30 ft x 12 ft) allows ample workspace for data collection equipment, load resistors, and other support equipment, all covered by a large canopy.
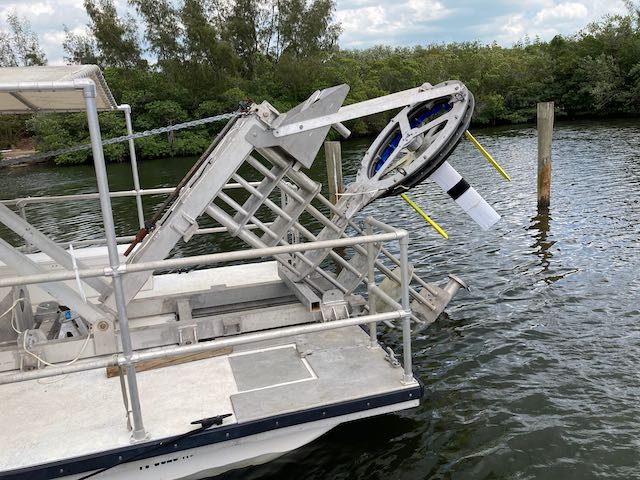
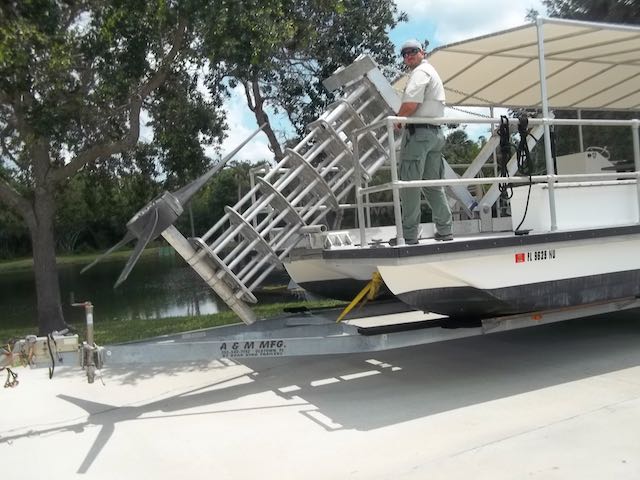
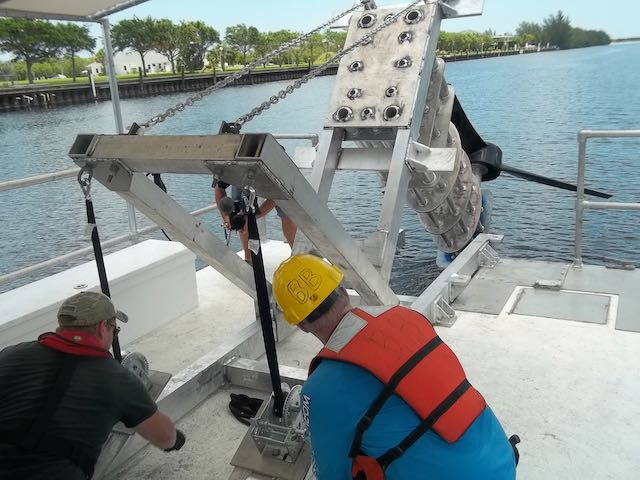
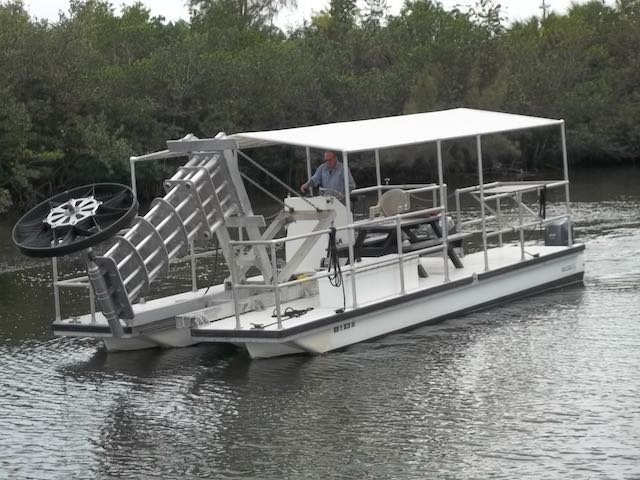
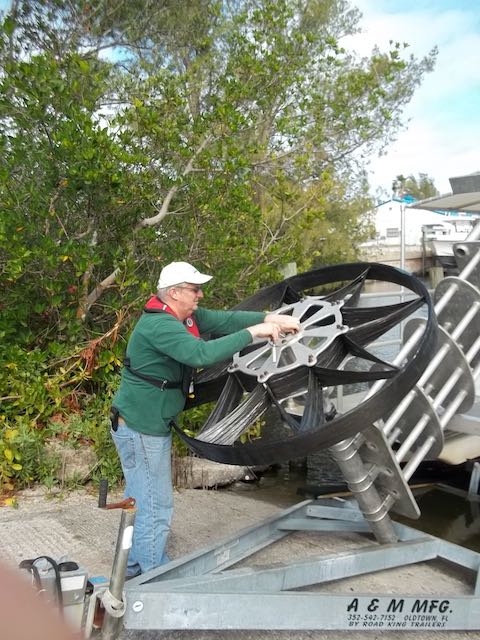
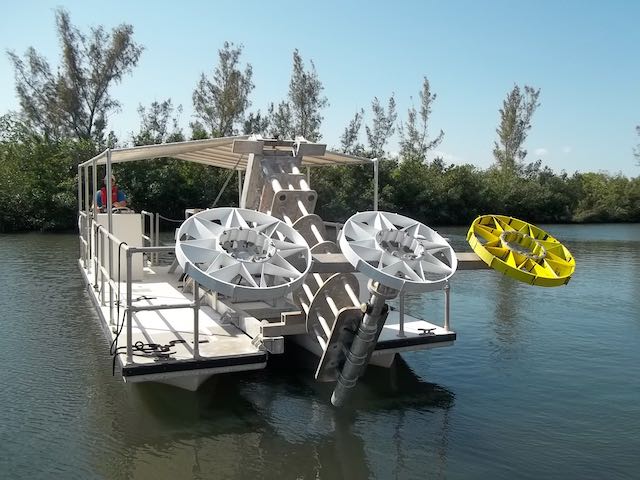
The RTD components are instrumented to measure drag, torque, and generator power production and may be recorded simultaneously or individually for component testing. The static rotor shaft utilizes strain gauges to measure both axial drag and torque and has been successfully used with three one-meter diameter rotors simultaneously. An instrumented pipe mount contains a two-axis strain gauge for measuring bending and a torsion strain gauge array for single-blade testing, built specifically for the rotor generating concept. A load resistor bank with various power resistors was built to provide a load to generator output so that power production could be measured. A data collection and storage unit were designed to receive and save the various sensor outputs, as well as speed over ground (GPS), an accurate time reference, and water velocity using an Acoustic Doppler Current Profiler (ADCP) mounted on the bow. The ADCP uses acoustics to determine true water velocity over the test item and allows for tidal flows to be incorporated into actual through-water velocities.
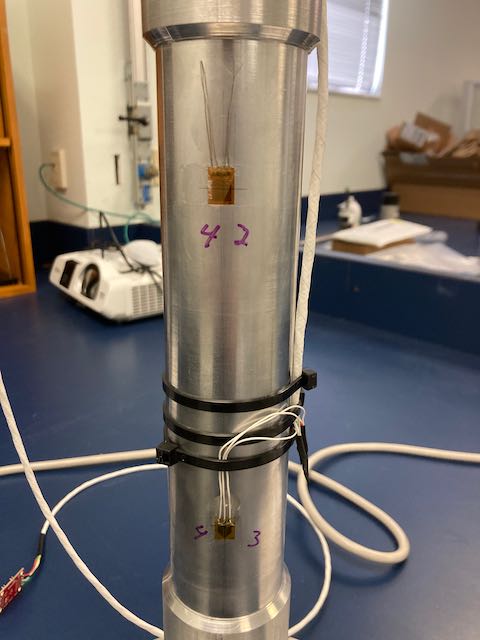
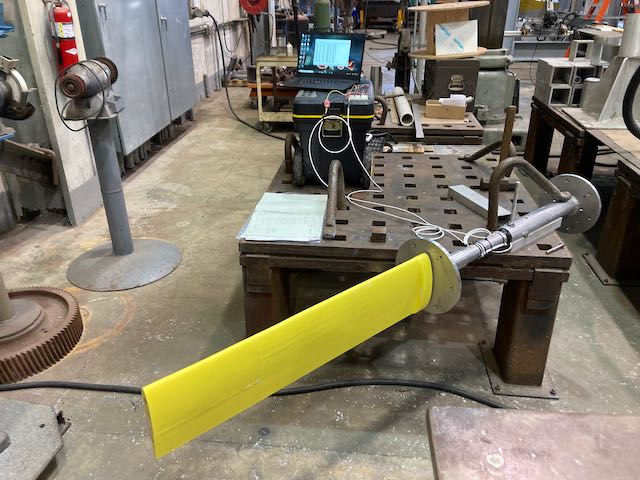
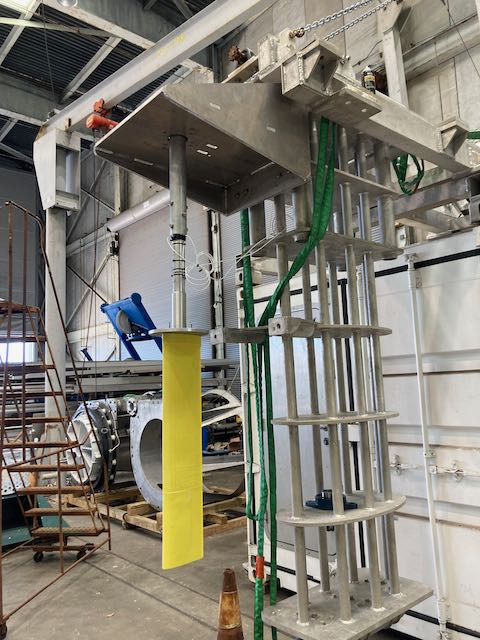
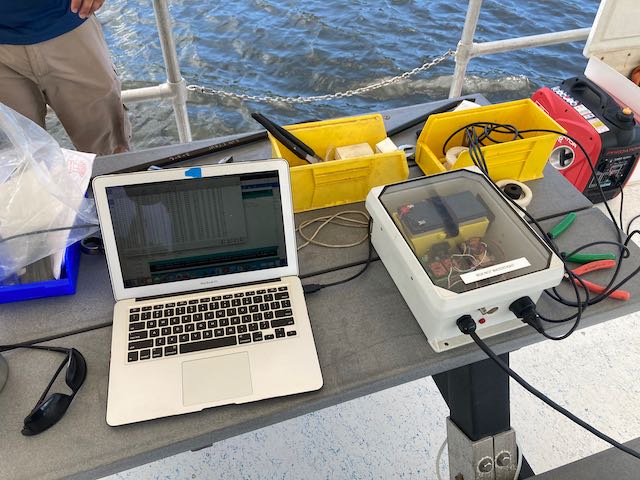
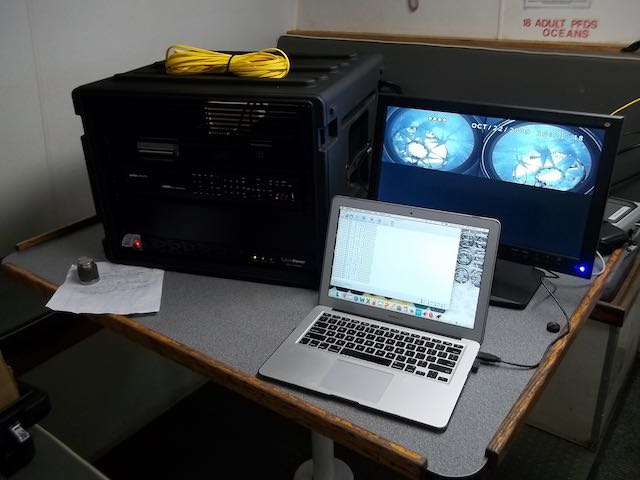
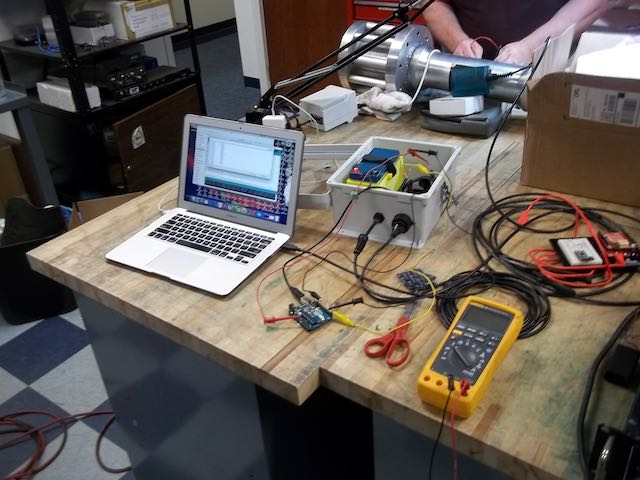
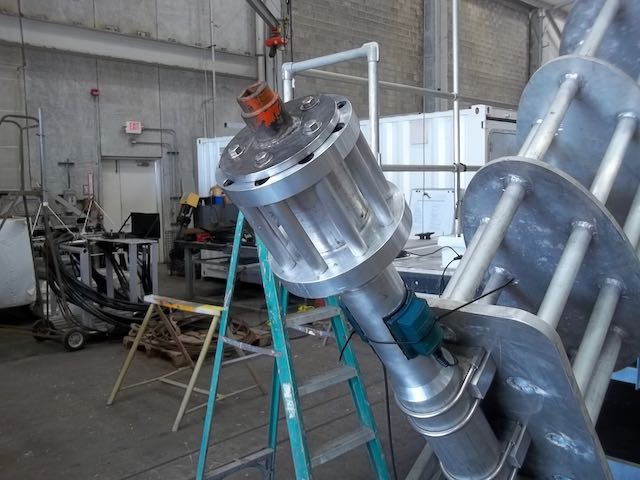
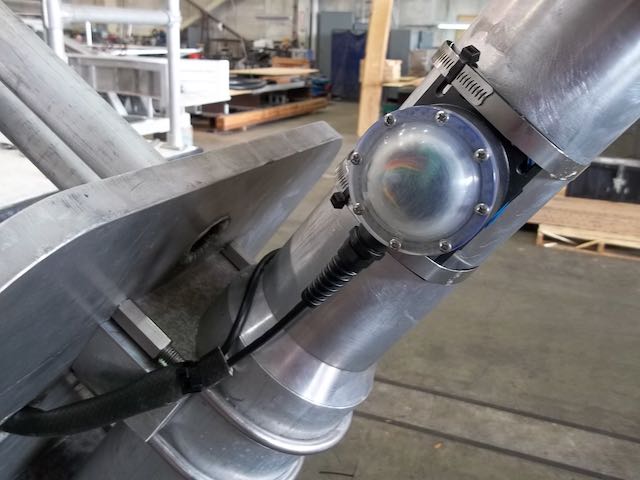
Design and Fabrication
Given the novel designs required for a river generator, Charybdis LLC has also invested in several 3D printing machines to streamline prototype development. The first 3D printed blades were made in 2018 to support initial coin testing and were modeled after a 3m woven rotor blade previously used in a university research program. The rotor was modeled and reduced in size to a 1-meter diameter unit. This rotor was printed in eight sections, given the limited size of the printer, and was mechanically fastened together and filled with epoxy and reinforcing rods. Similar 3D printed blades have subsequently been used throughout the project, including the new river device, and have proven quite durable and reliable at speeds in excess of 3 meters per second. This technology is also being used to design the break-away blade feature for debris.
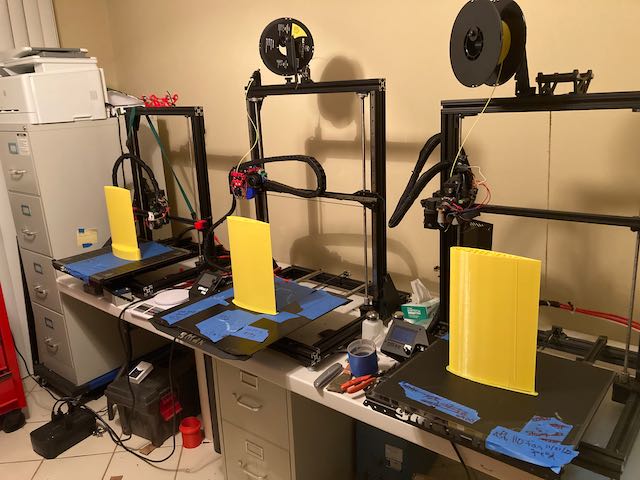
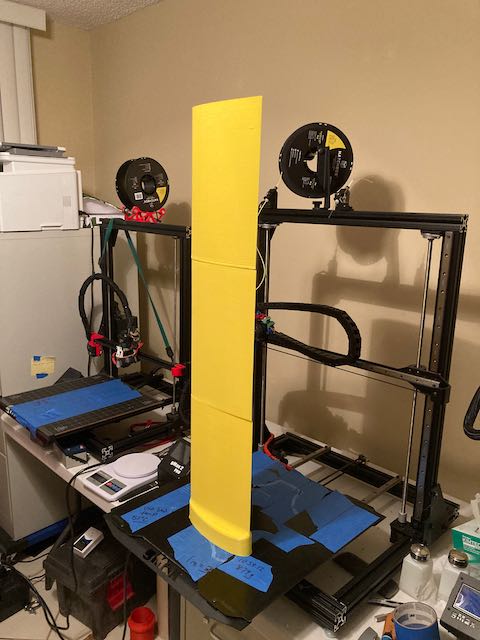
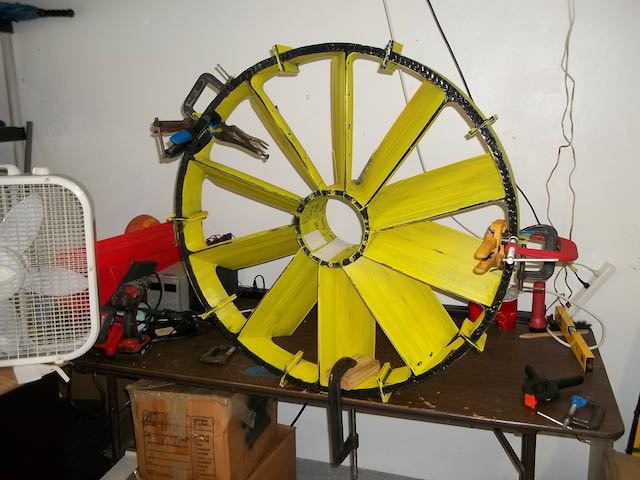
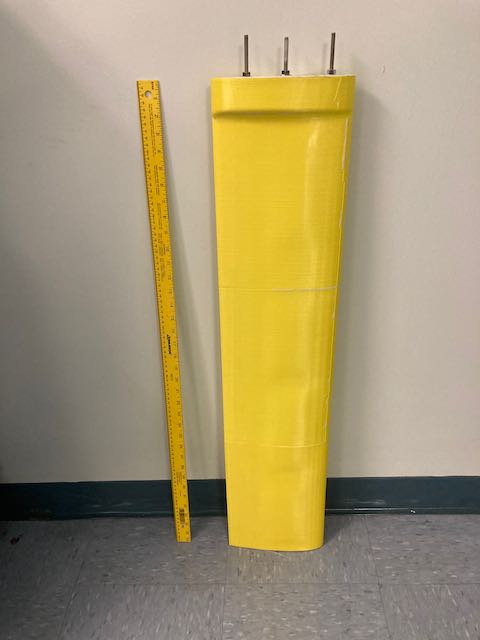
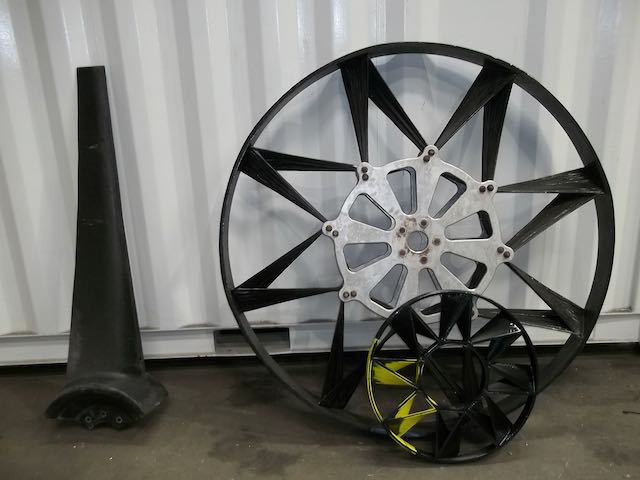
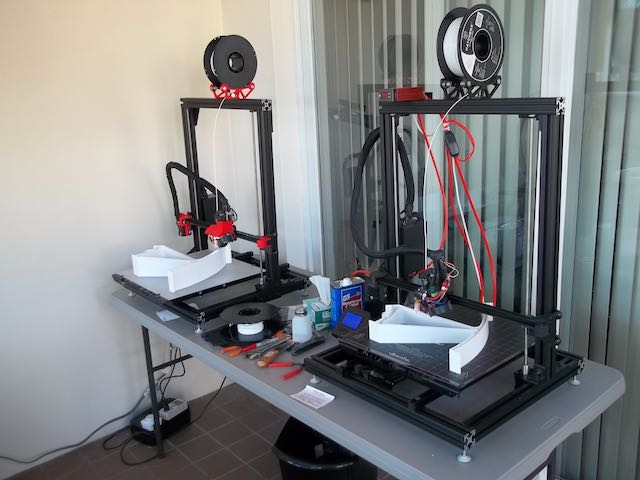
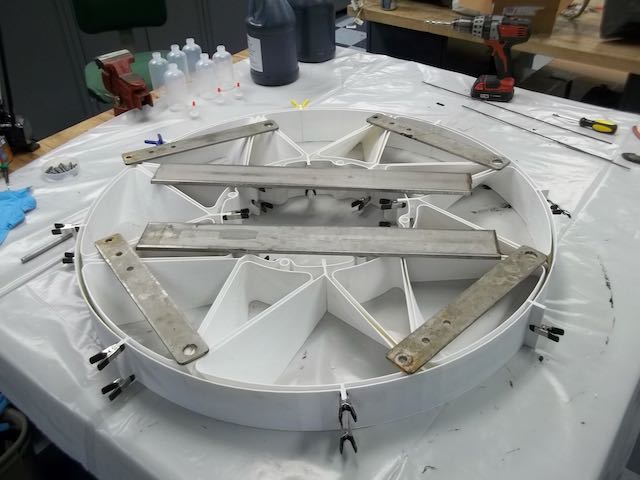
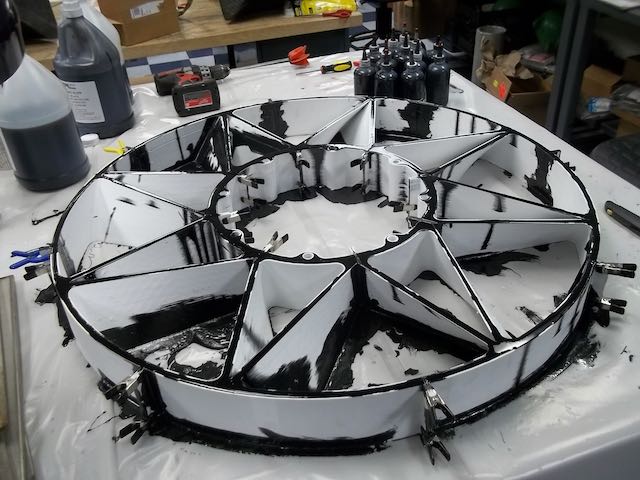